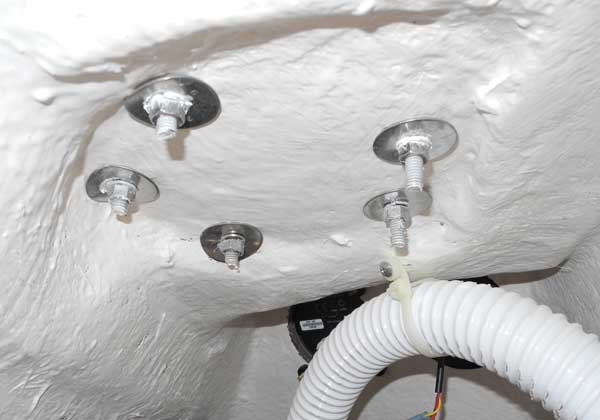
How To Use The Right Fastener
Based on an article by Don Casey
Anything you want to attach to your boat has to be fastened in some way. Today we have astounding glues that are stronger than the materials they bond, and some tapes are capable of joining railroad cars. Most of the time, though, mechanical fastening will be the attachment method of choice. Metal fasteners set the bar for strength, offer unmatched longevity, and most can be disassembled without destruction. Select wisely and install carefully to ensure your fasteners hold to their maximum strength.
Selecting the right fastener (see below) begins by assessing the load that will be placed on it. Any metal fastener will hold well against a sideways (shear) force. But with a tensile force pulling the fastener straight out, holding strength becomes increasingly dependent on the threads (or formed head in the case of rivets) holding the fastener in place. The load on lifting and towing eyes is almost entirely tensile — it is trying to stretch the fasteners or pull them from their holes. When the tide goes out, docklines start to tug upward on cleat fasteners. Pedestal seat bases pry up mightily on their forward fasteners, then on their aft ones as your body weight shifts in a chop.
In general, the weak link in the attachment of a fastener is the internal threads that the fastener's external threads engage. Threads cut by wood screws into wood, or by sheet-metal screws into fiberglass, lack the strength, consistency, and durability that machined threads inside a metal nut or other thick metal component can provide. Bolts or machine screws must be used to secure any component or piece of hardware essential to boat function and/or safety that might experience a load that will or could pull or pry it from the boat. In addition to nuts on the backside of the fitting, through-bolt mounting should include a strong backing plate made out of aluminum or stainless steel or, at the very least, heavy fender washers to spread the load.
The most common mistake when installing fasteners is to overtighten them, which either strips the threads or breaks the fastener. A stainless-steel 10/24 bolt has a maximum torque of less than 2 foot-pounds (22.8 inch-pounds), a force you can apply curling your fingers. A 1/4-20 bolt shouldn't be torqued beyond about 6 foot-pounds (75.8 inch-pounds). Even the 21-foot-pound maximum torque of a 3/8-24-bolt requires only wrist strength to apply. With regularly selling torque wrenches for under $10, there's no reason not to own one of these tools if just to gauge your own strength. Without long experience or the guidance of a torque wrench, snug threaded fasteners, then stop. The keys to fastener reliability are to select wisely; use lubricant, insulator, or thread locker when called for; install carefully; and tighten gently. Do these four things every time and all your fasteners will deliver their maximum strength